Tensile structures and large span membrane roofs for architecture
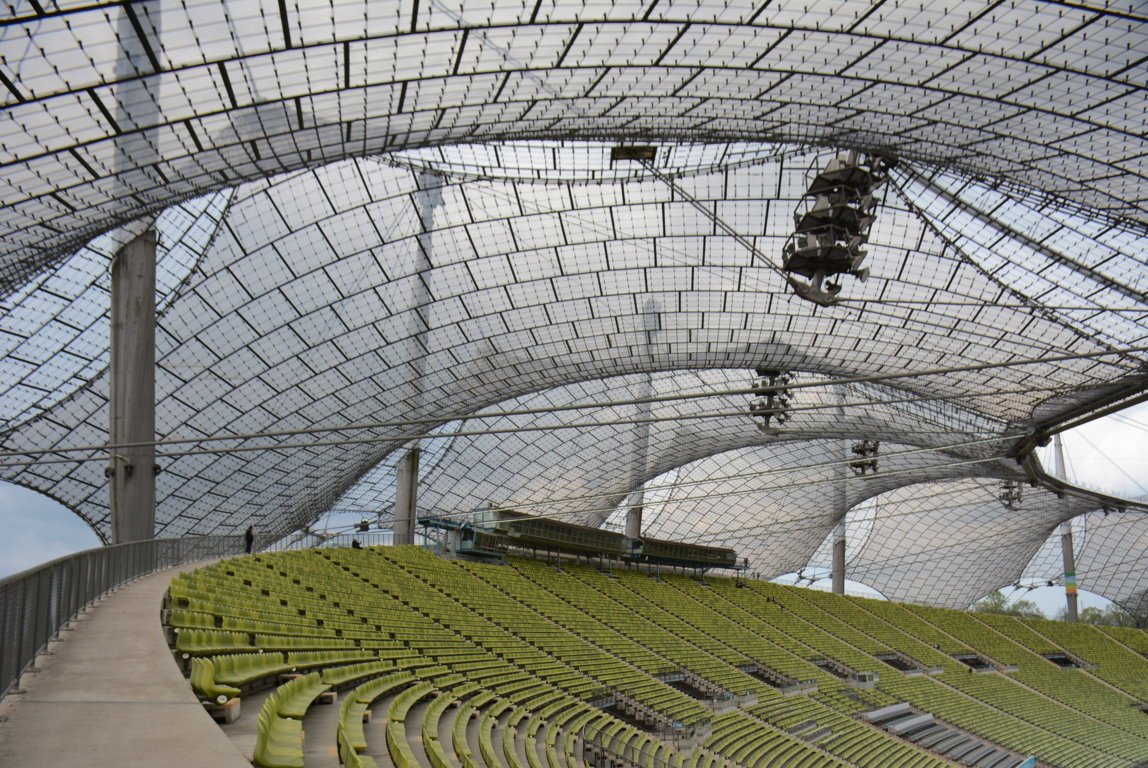

LIGHTNESS AND AESTHETIC VALUE
The tensile structures are the solution to cover large areas of complex shape by minimizing the materials used. In tensile structures, materials are used efficiently (tension and compression only). Thanks to specific supports, on existing buildings or through cable-stayed poles, it is possible to tension a membrane which, due to the “double curved” shape, will support external loads such as wind and snow and allows to cover large spans at very cmpetitive price compared to standard building technology, an iconic aesthetic result and a reduced environmental impact. Maco Technology is specialized in the design and construction of tensile structures in PVC coated polyester and/or PTFE coated fiberglass membranes, depending on the required performance and lifespan expected. In this guide we talk about:
- What are tensile structures?
- Differences between tensile structure and marquee.
- Typology of tensile structures
- Application of tensile structures
- Tensile structures: the advantages
- The materials of the tensile structures
- The details of the tensile structures
- The assembly of the tensile structures
- The legislation
What are tensile structures?
Definition
Tensile structures are made of elements design to absorbs only tension forces (membranes and cables). Pillars are usually hinged and therfore they works only in compression. For this reson, tensile structures are the most efficient building construction technology: they are effective and lightweight either form a structural and aesthetical point of view. For all these reasons, tensile structures are ideal to cover large span. On the other hand there are limitation of the shape: not all forms can be realized with tensile structures. Their shape is the result of the internal forces wich runs through their members, always in equilibrium.
Structural principle
Tensile structures are defined “form-resisting” o “form active” structures. If the form changes, the load bearing capacity changes too. To resiste external loads (wind and snow), membranes should have the typical double-curved configuration. Doble curved shape is the result of a form findg process which minize the fabric stresses starting from a given prestress level. The higher is the double curvature in the fabric, the better is for the efficiecy of the system which reduces internal forces. To learn more about how tensile structures works, please link to our blog.
Dfferences between tensile structures and marquees
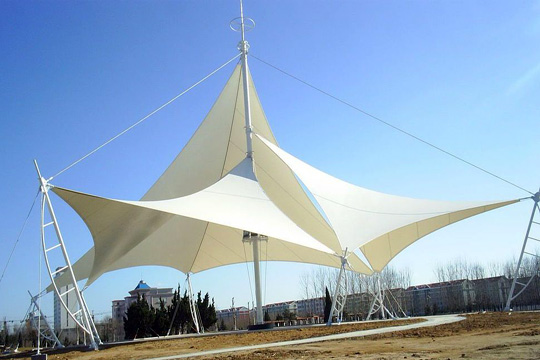
Tensile structures: all membrane, minimum structure
When someone think at a tensile structure, the first image pops up in mind is a stretched fabric or cable net, supported by cable-stayed hinged pillars (masts) which have the role to pre-stress the membrane and fix it to the foundations. In tensile structure nothing is useless or redundant: if fabric is damaged or a cable is disconnected, the form changes finding a new equilibrium of forces. The fabric is, in fact, either cover and structure of the roof at the same time. Tensile structure is by definition a form active structure: higher is the level of double curvature, lower are the stresses inside the members (fabric, cables, masts etc) and therefore at foundation. If you are interested we investigeted more deeply the differences beween tensile structures and marquees here in our blog.
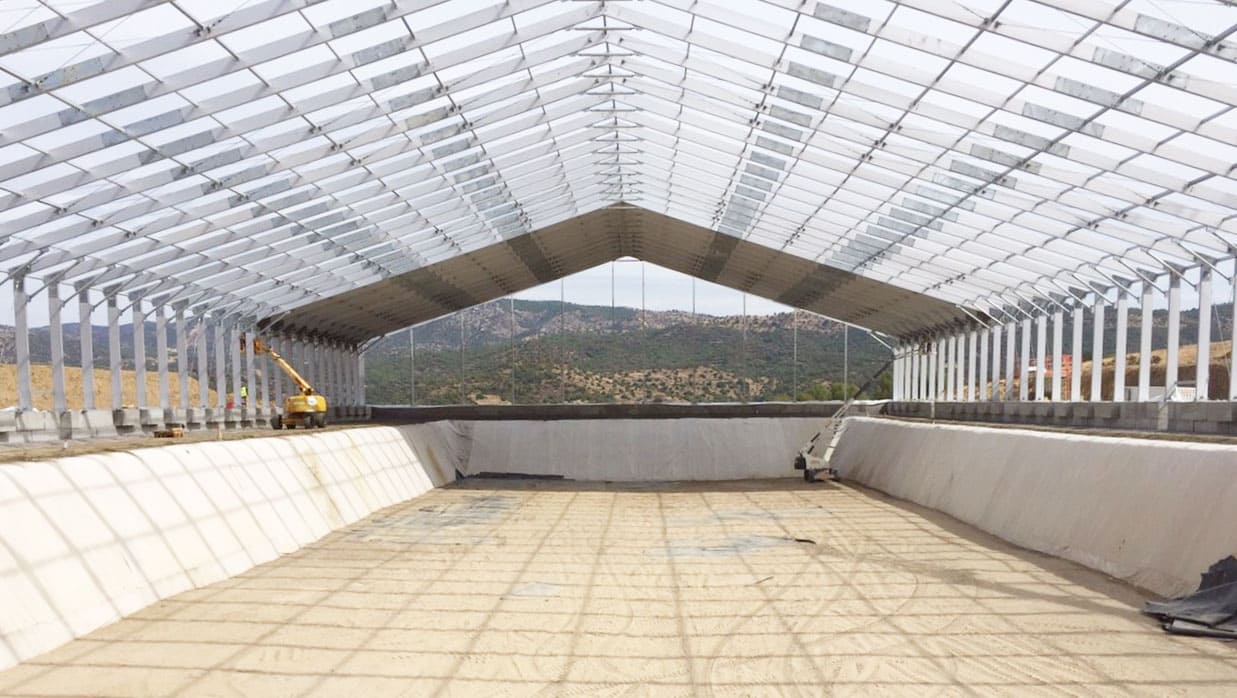
Marquees: supporting rigid frame and membrane as cladding
Marquees have a very clear structural principle: they consist of steel of wooden frame based on pillars and pitched rafters (portals) connected one to each other. This structure system is designed to carry the the vertical loads (snow, wind) as it happens for standard structural construction system. The fabric is only laying on top of the supporting frame, acting as a cladding: the prestress level in the membrane is pretty low and the geometry of the fabric is manyl flat (no double curvature). The prestress in the fabric is there only fo avoid fluttering, while the loads are carried by the frame. Marquees, can therefore be considered as standard building in which the envelope (usually bricks or insulating panels) is a memrbane. In the unlikly event of a damage to the membrane, the structural stability of the roof is not affected at all and the geometry remains the same. Marquees are modular and designd to be assebled in different configuration with a certin leverl of flexibility. The same is not possible with tensile structure which are design to work as a whole.
Typologies of tensile structures
The flexible parts of the tensile structures, ie the membranes and the cables, are arranged in space following the directions of the forces acting inside them. For this reason these structures are also known as “From-active”. The edges and the point connections of these elements influence the final shape that the cables and membranes can generate. For this reason, tensile structures can be categorized according to the types of support and, consequently, their shape. In the following classification extracted from Seidel, M. (2009) Tensile Surface Structures: A Practical Guide to Cable and Membrane Construction, Ernst & Sohn, Berlin, all types of tensile structures can be found which, juxtaposed, side by side or mirrored, give life to most forms of possible tensile structures.
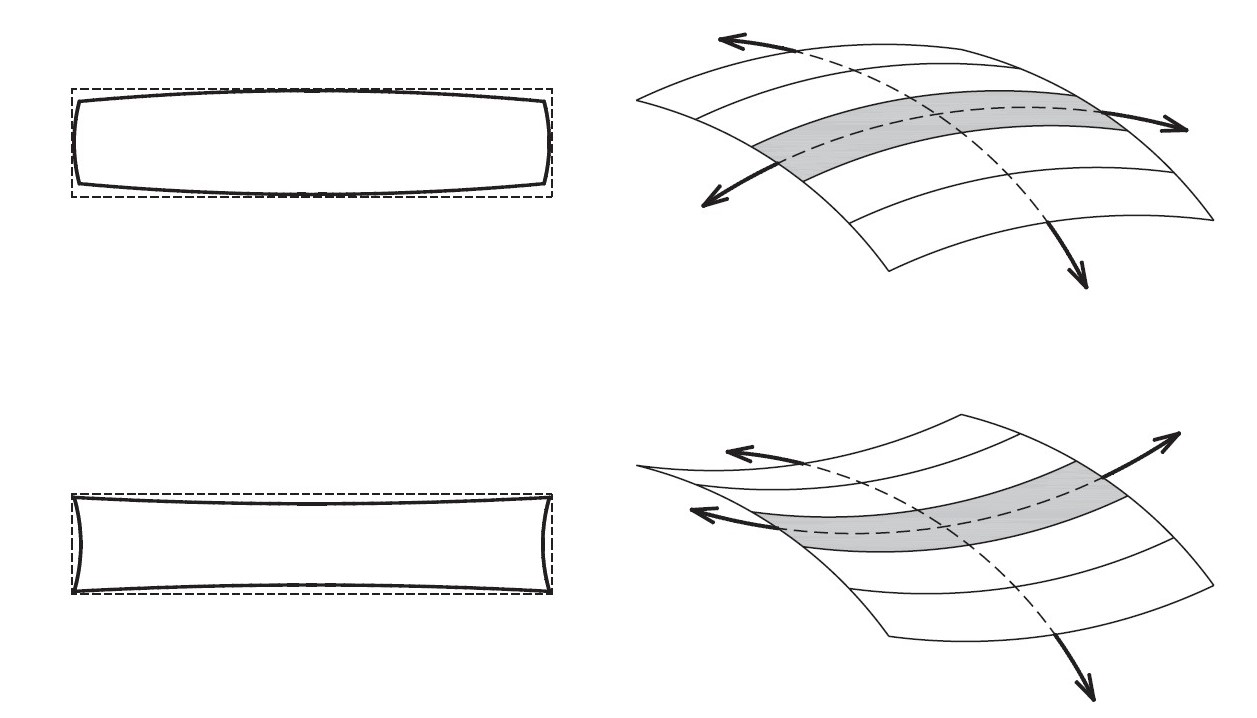
As is known, tensile structures have “double curved” surfaces, ie curved in two directions. The shapes of the tensile structures are divided into synclastic and anticlastic according to the direction of the double curvatures of the surfaces as shown in the side diagram (Taken from Seidel M. 2009). Surfaces with curvatures in the same direction are said to be synclastic, while those with opposite curvatures are anticlastic.

High or low point anticlastic surfaces. Here an example of the first category: conical structure with point tensioning.

Anticlastic surfaces supported for points with ridge or valley: here an example with ridge cable.
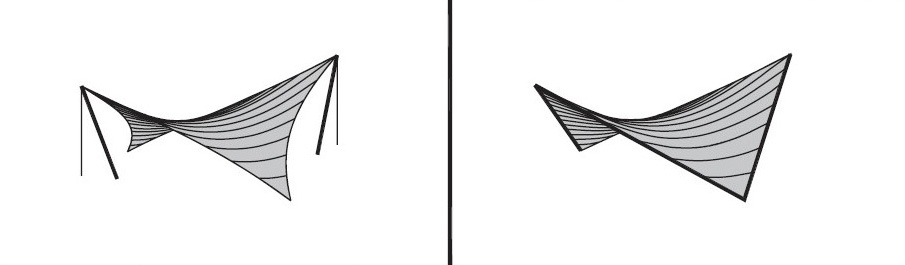
Anticlastic surfaces with high and low points tensioned by points or edges: hyperbolic or hypar paraboloid. Here is a typical example of a multi-point, high and low point structure.
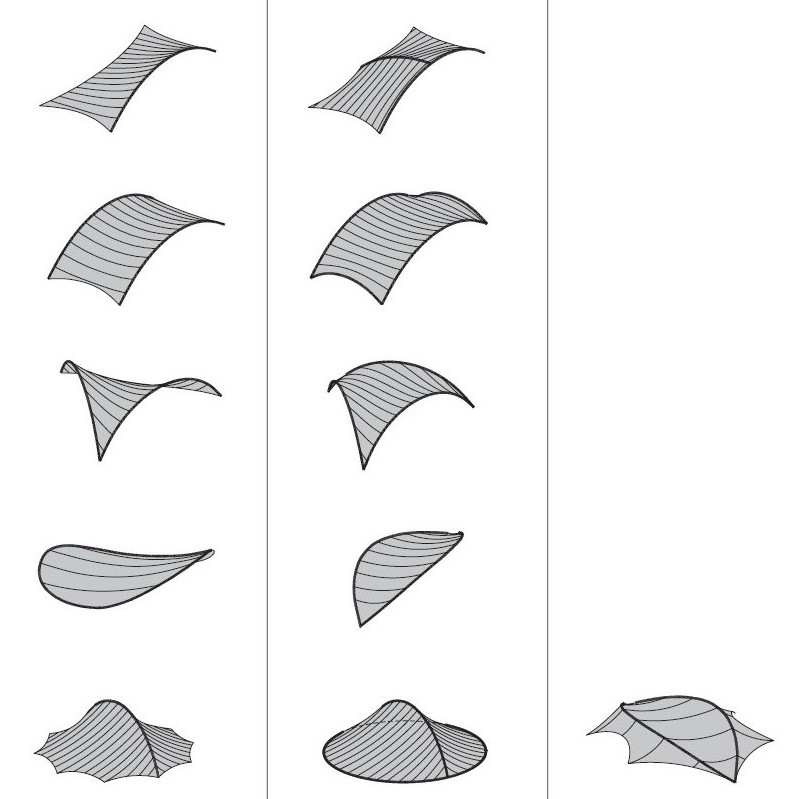
Anti-plastic surfaces supported with rigid arched edges in different configurations.
The geometric possibilities with this typology are several.
Here is an example with two parallel arcs and linear edges.
Here an example with parallel arches but free edges.
Here instead the typical example of a 4-arch structure, the so-called cross vault structure.
Here a structure composed of several edge arches and intermediate support to the membrane.
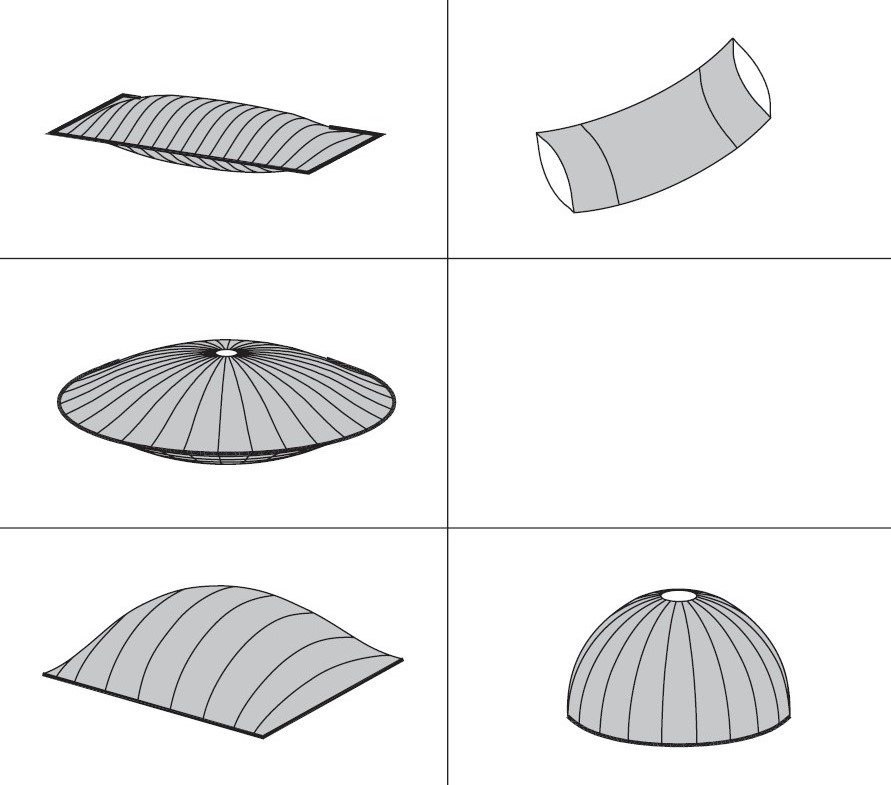
Air-supported synchlastic surfaces.
Here is an example of ETFE cushions with linear edges.
Here is an example of ETFE cushions with curved edges with parallel arches.
Here is an example of ETFE cushions with curved edges with inclined arches.
Here is an example of an airhall with a rectangular perimeter.
Here is an example of a pressostatic cover with a circular perimeter for a biogas digester.
Application of tensile structures
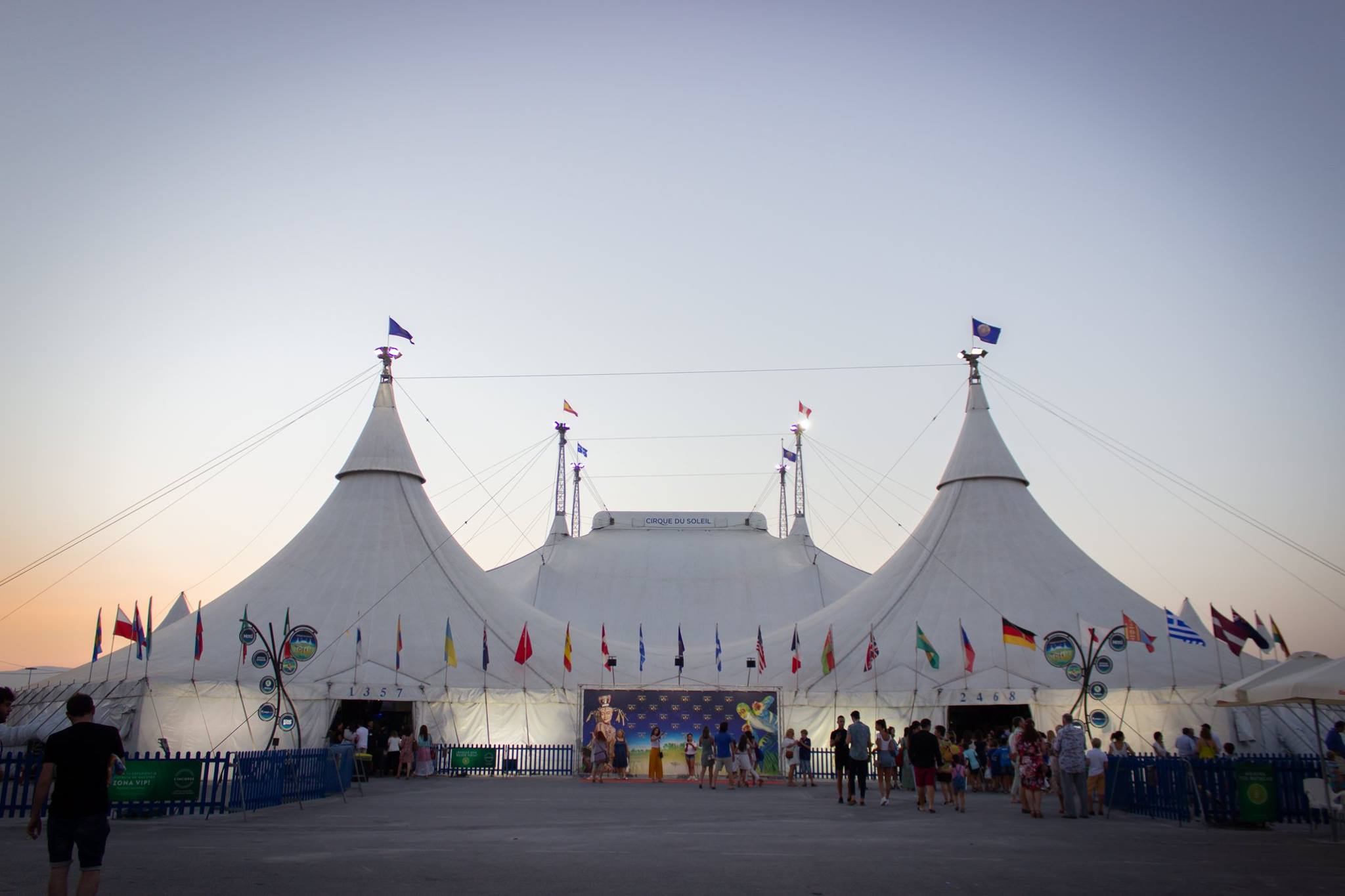
Covers for circuses
The historical origin of the tensile structures in architecture dates back to the tents used as a dwelling by the nomadic populations among which the Yurt tents of Mongolia or the Teepee of America are known. In more modern times, the first large tensile structures are those used by circus companies to set up their shows. The evolution of these roofs has led to the current “chapiteau” which can reach truly impressive dimensions: Cirque du Soleil for example uses structures over 50 meters in diameter, with antennas of 25 meters and height of the cusps of 19 meters. These roofs are tensioned by over 500 cable-stayed perimeter pillars.
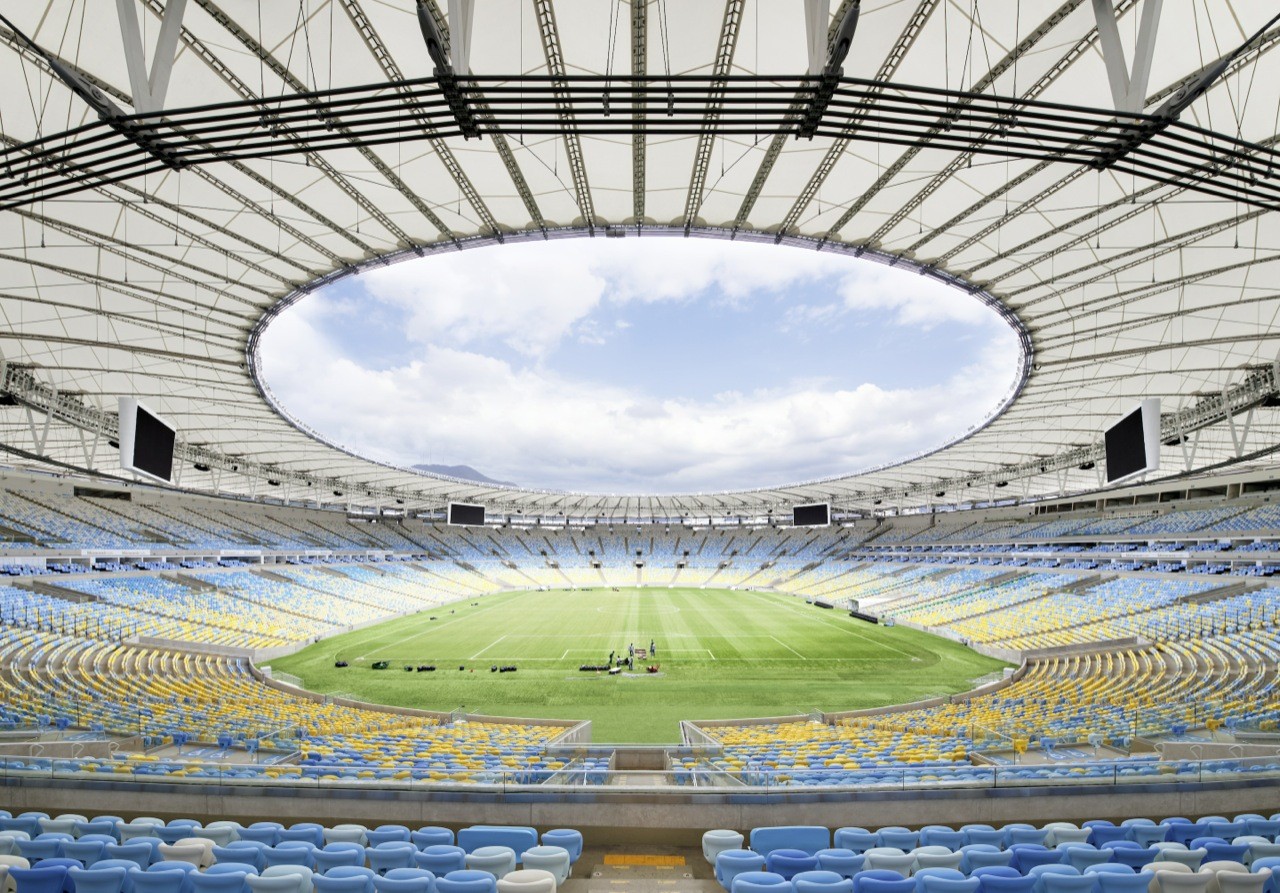
Stadium covers
Tensile structures reach their maximum expression in stadium roofs. In these cases it is in fact necessary to cover large spans at the lowest possible weight in order not to burden the substructures and foundations. Furthermore, having to leave the view of the playing field free from any obstruction, it is necessary to adopt a structural principle capable of cantilevering. This is the case of the “spoked wheel” principle or bicycle wheel which consists of a compressed outer ring and a tight inner ring, connected together by cables in traction. The result is a unique tensile structure that embraces the entire covered arena and must be erected in one go through the so-called “big lift”.
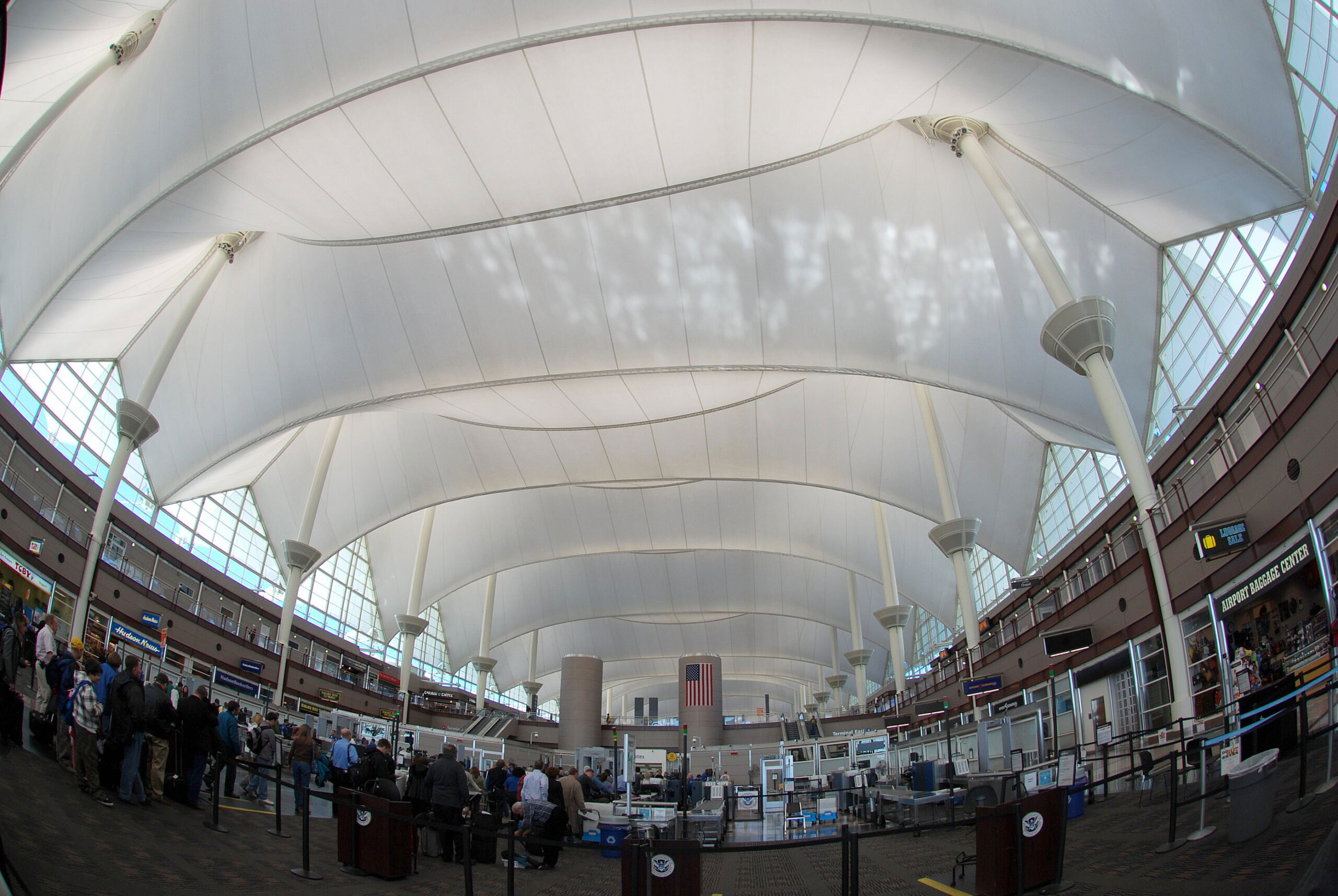
Coverings of walkways and atriums
Linear coverings, big span, covering walkways for example in shopping centers, airports or exhibition facilities, can be covered with tensile structures that allow excellent diffused lighting, a very strong aesthetic impact and a relatively “light” load on the supporting lateral buildings thanks to a point-support structure. To obtain the same results with traditional translucent materials such as glass, a load-bearing substructure based on massive reticular beams would be required, which would compromise the general aesthetic result.
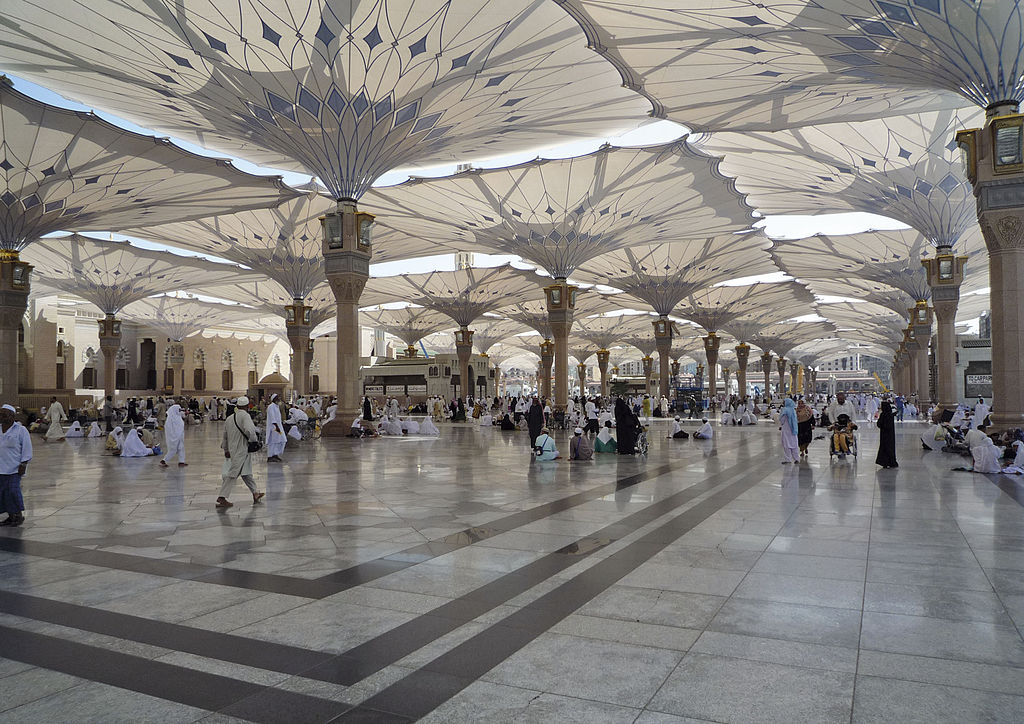
Squares covers
Large squares can be covered with free form tensile structures in order to armonize with the pre-existing structures or the most complex architectural geometries. In this case, the roof becomes a an unique urban furniture, iconic and easily distinguishable from the technological language of the construction system which is clear and different form the exsisting buildings. A similar result could hardly be obtained by applying construction systems based on beams and pillars which would necessarily require a well-defined and regular geometric rythm.
Advantages of tensile structures
Economic benefits
Tensile structures use construction materials in the most efficient way: cables and membranes work only in traction while the supporting structure is usually only compressed. This allows to minimize the use of materials. Furthermore, the lightness of the construction system and its flexibility during operation allows the tensile structures not to be subject to the seismic legislation which would lead to an increase in the load-bearing sections and, consequently, in cost. For large dimensions, therefore, tensile structures are certainly the cheapest construction system. On small or medium-sized projects, however, it depends on the shapes and materials selected. PVC coated polyester tensile structures can be very competitive.
Here you can read an in-depth analysis about the cost of PVC coated polyester membranes
Structural advantages
The tensile structures need to be anchored to the ground and transfer to it only tensile or compressive forces in very small areas. It is often said that the mass that the tensile structures do not have above ground is what must be placed in the foundations to allow the structures to be correctly prestressed according to the design load. Nothing more true! However, in on one hand compression is easily absorbed by simple foundations, traction, on the other hand, must be managed through anchors, log bolts or large foiundation. When the foundations become too large, the correct design allows the creation of closed systems, such as the spoked wheel used for the roofs of the arenas, which do not transfer loads to the ground. The lack of mass and the flexibility of the structural elements used, allows the tensile structures to go, in most cases, in derogation as regards the seismic regulations. The tensile structure will therefore be able to oscillate and move in the event of an earthquake, dissipating the energy introduced, without being damaged.
Environmental benefits
The lightness of the tensile structures means a lower environmental impact in terms of waste of resources and impact on the gorund. Furthermore, by definition, tensile structures are dry-assembled architectures, totally demountable and potentially relocatable in another place if necessary or if new needs arise. Reuse in therefore a must, rather than just recycling, which is not always really possible. Tensile structures are therefore flexible architectures capable of being modified and adapted over time if needed. It is impossible to do have the same approach with traditional construction systems which are by definition fixed and no longer removable.
The materials of tensile structures
In the blog we have a page dedicated to the description of the main textile materials used for tensile structures. In this guide, however, we quickly mention the two most popular materials for this type of application: PVC coated polyester and PTFE coated glass fiber.
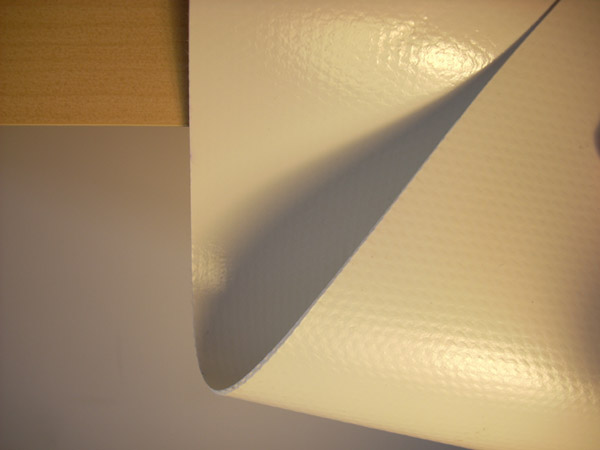
Polyester fibre PVC-coated membranes
It is the most widespread, most versatile and economical material in the world of textile membranes for architecture. It consists of a polyester fiber fabric base to which a PVC coating is added containing various additives capable of guaranteeing the flexibility of the final result, its color, resistance to fungi, UV rays and flame. These materials are usually lacquered on the surface by a transparent PVDF layer which helps to maintain surface cleanliness and durability. The performance range of PVC coated polyester membranes is enormous, ranging from materials for small roofs with guaranteed durations of 5 years up to highly performing materials guaranteed for 20 years.
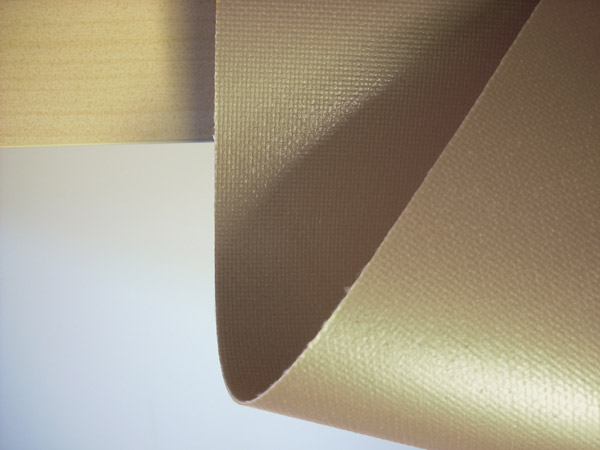
PTFE coated fiberglass tensile structures
They are the most performing and long-lasting membranes with a life expectancy of over 20 years. The glass fiber, very resistant and stable to traction, guarantees excellent structural performance at a light weight. The PTFE (Teflon) coating ensures a much longer duration than PVC and a much greater cleaning of the membrane. The main limitation of this product lies in the cost, much higher than the polyester / PVC membranes, in the packaging speed (much lower than PVC) and in the impossibility of bending the material beyond a certain radius during transport as the glass fiber could break compromising the mechanical performance.
The details of the tensile structures
The tensile structures are an assembly of details. Each component is designed to withstand a certain force oriented in a certain way. Each element aligns itself in equilibrium with all the others in a geometry that can be one and only that. For this reason, the details are themselves the tensile structures and, if well developed, make the difference. Below, we quickly illustrate two crucial details in tensile structures: the corner plates and edge cables.
The corner plates
The corner plates have the function of transferring the forces coming from the cable-stayed pillars uniformly on the membrane surface. The plates must be able to orient themselves freely according to the forces and must reach the equilibrium between the membrane forces acting on the plane tangent to the membrane and the point forces of the edge cables acting in axis with them. This element is therefore crucial for the success of the tensioning and must be geometrically designed for each single membrane. The plate is made up of 3 parts: the connection to the pillar usually by means of a hinge, the connection to the membrane by means of plates and the connection to the cables through correctly oriented bushings. If you want to obtain a top quality result, it is almost impobssible to standardize or replicate the same plates on different membranes . For this reason, at the design level it is necessary to speed up the production of these details in order to be able to make them parametrically. Here an example of parametric design of the plates of a tensile structure.
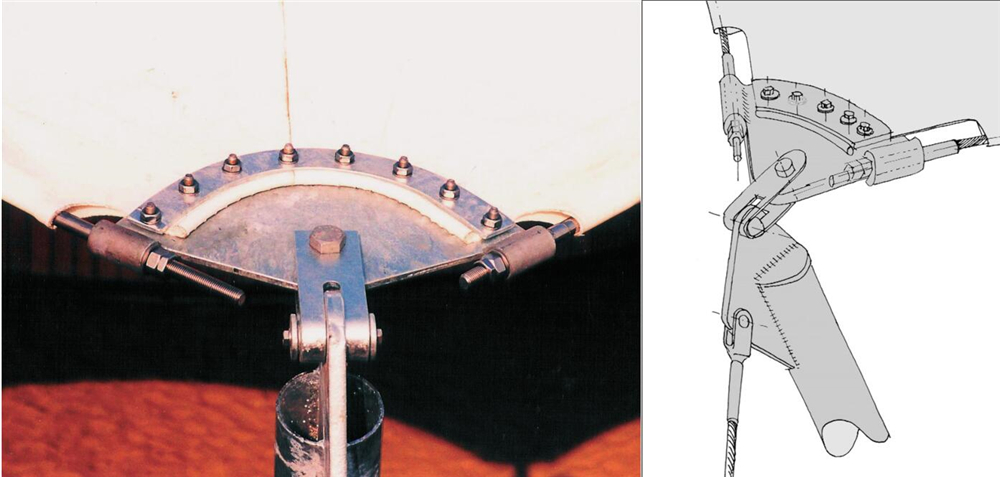
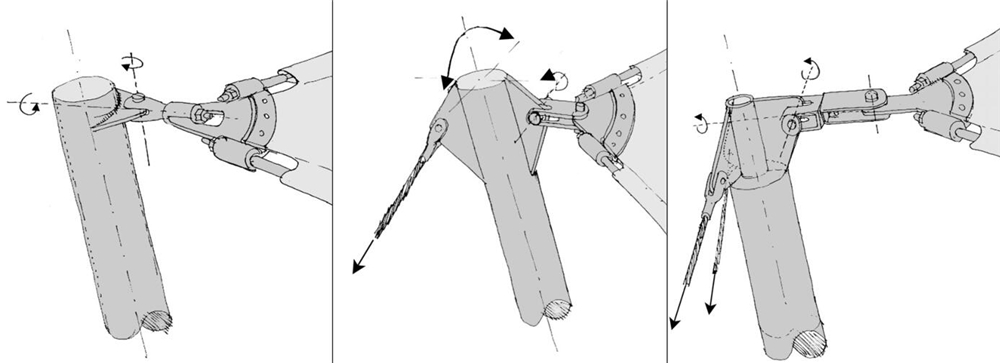
The edges of the membranes: cables, plates and fastening
The edges of the membranes can be tensioned with edge cables, through flat elements with rigid elements or through ligations both with cables or rigid elements. The edges must be prepared in order to guarantee a perfect seal, also taking into account any sliding and stretching of the material during assembly and operation. An incorrect design of the edge details could result in perimeter defects and, in the worst cases, in membrane breaks in case of unexpected stress peaks.

In most cases, the membrane hosts stainless steel wire inserted inside reinforced pockets.
The assembly of the tensile structures
The shape of tensile structures derive from to the state of pretension introduced in the membrane and in the cables. Therefore, compared to all traditional architectural assemblies in which the elements are placed in position by geometry and remain in equilibrium due to their own weight, in the case of tensile structures the objects find their position following a balance of forces given by the elements prestress: cables and membranes in tension, pillars in compression. The assembly must be done by expert operators as the geometric and structural result is bound to the correct introduction of the project loads and to the respect of assembly phases that should follow a strict procedure. Instruments capable of introducing the required forces must also be present on site, possibly measuring them. Alternatively, the prestress state can be predicted based on the expected strains. All the tense elements, in fact, are “compensated” products, ie slightly smaller: as a result of the tension introduced and as a result of the elongation of the materials until reaching the design positions, it can be assumed that the correct pretension has been introduced.
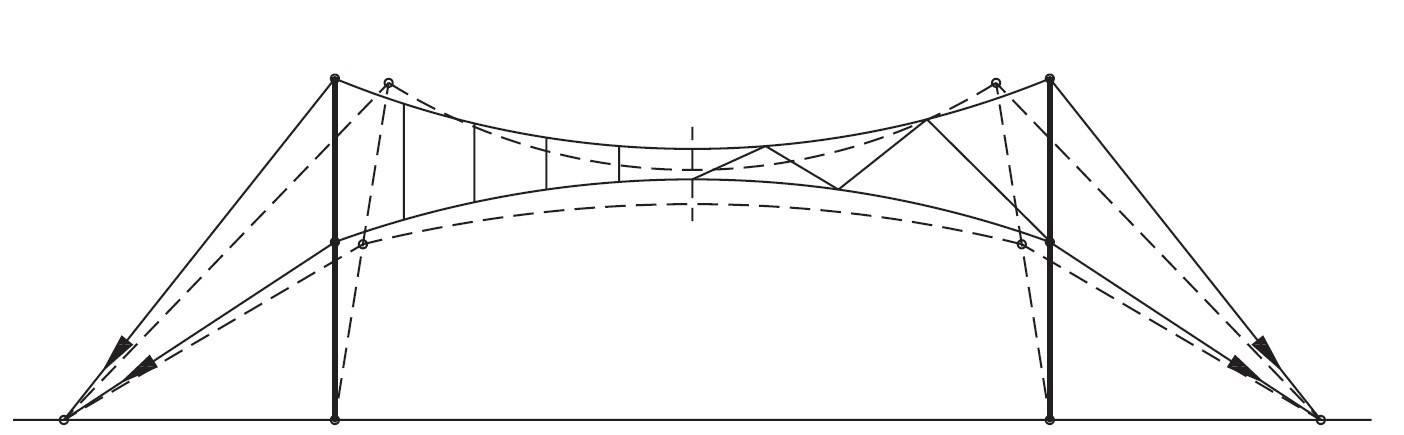
The elements that compose tensile structures are mainly hinged together and free to find their position following the tensional equilibrium. However, there are several or even infinite shapes in equilibrum. The correct assembly has the objective of achieving the design balance through strategies aimed at introducing the expected prestress into the membranes and cables. The simplest and most effective strategy is to use the cable-stayed pillars shown in the images above and below. In the image above, the system is schematized in plan and represents the tensioning of a cable beam through the inclination of the cable-stayed pillars.
The image below, on the other hand, shows the assembly procedure of a typical tensile structure with high and low points (hypar) in which, with the same procedure, the high points are first placed in position and only in a second step, the low points are tensioned. The order in which these steps are done is fundamental. In fact, if one proceeded first with the positioning of the low vertices and only after the high ones, a different shape would be obtained, certainly more “flat” and not in conformity with the project. To learn more about this issue, refer to the article on our blog: The importance of correct assembly in tensile structures.
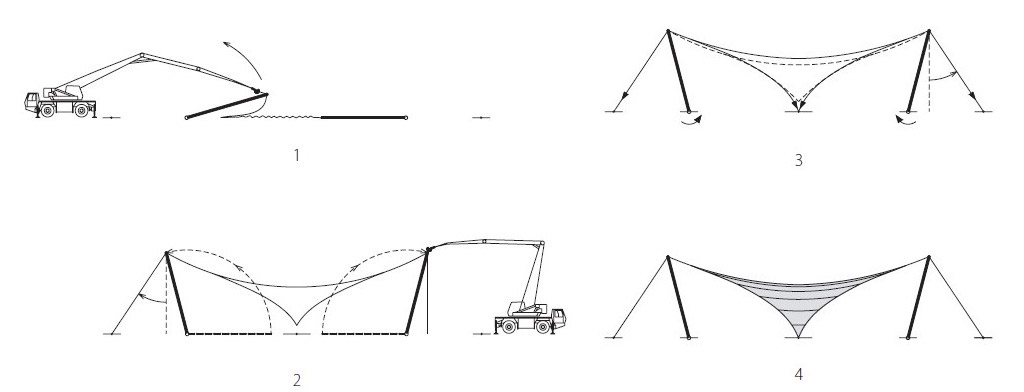
The legislation about tensile structures
At the time this article was written (January 2021), there was no Eurocode on tensile structures that fully regulates these constructions and not even a specific national regulation. In the absence of a specific Eurocode and a specific national legislation, the sector of tensile structures and marquees is mainly regulated by the regulations for temporary structures due to the temporary nature that generally characterizes this type of buildings.
The legislation concerning temporary structures
The UNI EN 13782: 2015 standard “Temporary structures – Tents – Safety”, which recently replaced the UNI 10949: 2001 standard “Safety of equipment for fairs and amusement parks – Tents, temporary and / or itinerant textile structures – Design, construction , assembly and maintenance ”, specifies the safety requirements relating to the design, calculation, construction, installation and maintenance of tents installed on a traveling, temporary basis with a covered area greater than 50 m2. The standard also applies to multiple small tents, which are not normally covered by this standard, which are installed close together and which together cover an area greater than 50 m2. In addition, reference can be made to the UNI EN 15619: 2014 standard “Textile substrates coated with rubber or plastic materials – Safety of temporary structures (marquees) – Specifications for coated textile substrates intended for marquees and similar structures”. The standard specifies the characteristics, requirements and test methods for coated textile supports intended for mobile and temporary tents for local structures or open buildings, for example markets, hangars, tent halls, stands, with the exception of camping tents, and for similar structures.
The standard attempt for tensile structures
For engineers and designers, the UNI U50.0.299.0 standard tentative norms “Tents-structures, tensile-structures, near-structures. Instructions for calculation, execution, testing, use and maintenance” still represents a valid reference when dealing with the strength, service, safety and durability requirements of tents-structures, tensile-structures and near-structures. In addition, it provides information on the quality of the construction materials and products used and the level of accuracy of the site operations necessary to comply with the assumptions defined in the design rules. This norm does not normally deal with structures with a covered area of less than 40 square meters such as market umbrellas, beach umbrellas, camping tents, sun tents and covers mounted daily, etc.