By Brian Burton
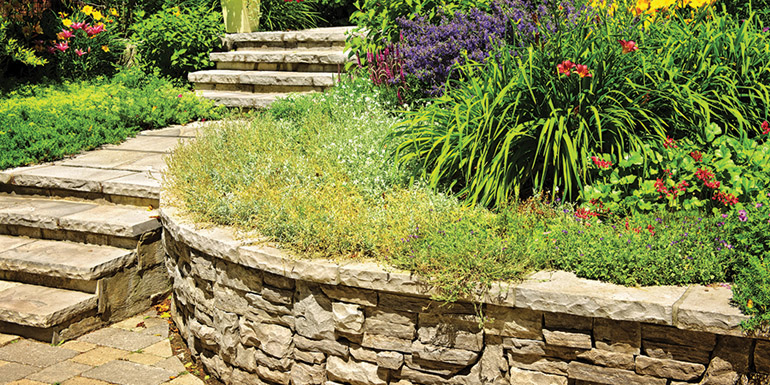
Conventional or gravity segmental retaining walls (SRWs), referring to manufactured retaining walls, as opposed to natural stone walls, effectively limit the movement of the soil behind them, primarily by the weight of their blocks. The maximum wall height of a single-depth wall is typically directly proportional to its weight, width, batter (face slope), soil condition, and site geometry. (Contractors should, in all cases, refer to the manufacturer’s instructions for specific recommendations.) The theory behind these retaining walls is to effectively alter the landscape to increase the area of usable land. On occasion they may be used in cases where there is a very steep or rapid change in the site grading. Retaining walls actually have an extensive history dating back to the introduction of primitive agriculture. These early efforts to improve agricultural production often used readily available local materials to alter the existing natural terrain and drainage patterns.
The basic concept of using the force of gravity and friction resistance based on material shape has been employed in many noteworthy civil engineering and construction projects throughout history with great success. For example, the Egyptian pyramids, most of which are considered to be megalithic structures, were constructed from huge blocks of stone ranging in size from five to 50 tons. Almost all of these structures, which were constructed without mortar, are carefully shaped gravity SRWs. After placement, the blocks or walls were moulded into shape with masonry tools and chisels.
Another example is the Great Wall of China—a raised roadway that stretches for thousands of miles across Asia—which was built by constructing two gravity retaining walls several metres apart. The space in between the walls was later filled with soil and stone to create a roadway. In a similar manner, Hadrians Wall, built by the Romans in AD 122 to “separate Romans from the barbarians,” used the same concept. It involved the construction of a 4.57-m (15-ft) high, 117.5-km (73-mi) long stone-barrier wall across Northern Britain.
Off the wall
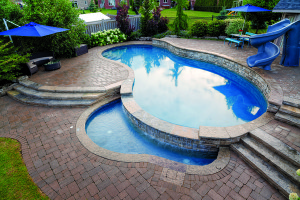
Over the past 40 years there have been tremendous changes in the way retaining walls are designed and constructed. The first wet-cast prefab concrete walls were introduced shortly after the end of World War II and were the walls of choice for many years, although timber walls did hold a share of the market. Dry cast segmental concrete block walls were introduced in the ’80s. A few years later, the industry saw the introduction of various plastic components such as geogrids, geomembranes, and geosynthetics, which improved performance and reliability when used in conjunction with retaining wall units.
In more recent times, engineers typically used wooden-timber walls, cast-in-place concrete, and precast concrete panels to construct earth retention systems to provide steep or vertical surfaces. These materials and construction techniques generally contributed to an imposing industrial appearance and, in the case of timber walls, had an expected life span of only 10 to 15 years before replacement was required.
Note: Wooden retaining walls were usually treated with creosote, a poisonous oily liquid obtained from the distillation of coal tar. Crude creosote oil, also called ‘dead oil’ or ‘pitch oil’ has been used as a wood preservative since 1916 for fence posts, hydro poles, railroad ties, etc. The toxic component, polyaromatic hydrocarbon (PAHs), is considered an environmental hazard. On occasion, contractors may be required to remove or dismantle existing wooden retaining walls and as a result, may come in contact with potentially hazardous materials. Although these systems are probably not as environmentally sensitive as when they were originally installed, contractors should still take the necessary steps to limit exposure to creosote. Normally it is considered good practice to limit disruption of the adjacent soil to the greatest degree possible. In addition, based on site conditions, contractors may consider personal protection in the form of gloves or masks. In some cases, the building permit or local municipal regulations may apply or the contractor may wish to inquire with the local authorities. The same may be true for disposal and transportation.